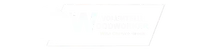
The Windsor of Chairs
11/1/2024 | 26m 46sVideo has Closed Captions
Host Charles Brock is joined by master Windsor Chairmaker Greg Pennington.
Greg Pennington is a master Windsor Chairmaker. He's also a master teacher of the art and an influencer at the center of a specialized genre of woodworking.
Volunteer Woodworker is presented by your local public television station.
Distributed nationally by American Public Television
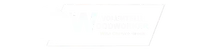
The Windsor of Chairs
11/1/2024 | 26m 46sVideo has Closed Captions
Greg Pennington is a master Windsor Chairmaker. He's also a master teacher of the art and an influencer at the center of a specialized genre of woodworking.
How to Watch Volunteer Woodworker
Volunteer Woodworker is available to stream on pbs.org and the free PBS App, available on iPhone, Apple TV, Android TV, Android smartphones, Amazon Fire TV, Amazon Fire Tablet, Roku, Samsung Smart TV, and Vizio.
Providing Support for PBS.org
Learn Moreabout PBS online sponsorship(bright folk music) - Welcome to the "Volunteer Woodworker."
I'm your host Charles Brock.
Come with me as we drive the back roads, bringing you the story of America's finest woodworkers.
(bright folk music continues) (car door slams) (bright folk music continues) We're going to Hendersonville, Tennessee to meet Greg Pennington.
Greg is a master Windsor chairmaker.
He is also a master teacher of the art.
He's an influencer at the center of a very specialized genre of woodworking that is attractive to woodworkers with a dream to someday be a Windsor of chairs themselves.
Let's meet Greg Pennington.
- [Announcer] "Volunteer Wodworker" is funded in part by: Since 1970, Whiteside Machine Company has been producing industrial-grade router bits in Claremont, North Carolina.
Whiteside makes carbide bits for edge forming, grooving, and CNC application: learn more at whitesiderouterbits.com; Real Milk Paint Company makes VOC-free nontoxic milk paint available in 56 colors: milk paint creates a matte wood finish that can be distressed for an antique look; (relaxed folk music) Good Wood Nashville designs custom furniture and is a supplier of vintage hardwoods; Keri Price with Keller Williams Realty has been assisting Middle Tennessee home buyers and sellers since 2013; Mayfield Hardwood Lumber, supplying Appalachian hardwoods worldwide; Anna's Creative Lens.
- Greg Pennington.
- Hi.
How you doing?
- I'm doing great.
I just love coming to your shop.
Your shop just reeks of chair making.
- Oh, thanks.
It's what I love to do.
And been doing that now for about 21 years, and I can't think of anything else I'd rather work on other than a chair.
- Well, it has great utility.
- Yeah.
Oh yeah.
- I mean, one is holding each of us up right now.
- Yep.
They're what I call chairmaker perfect.
They don't have to be perfect.
There's no perfect human.
So, you know, the anatomy of these chairs are, you know, they can be way off and still feel comfortable.
- Well, chair making is not the only woodworking that you do though.
- Right, I've done, you know, cabinets and work benches, and I've built a shop and everything, you know, outta necessity.
But the chairs are my one true love.
That's what I, always, at the end of the day, I want to go back to making chairs, for sure.
- Well, one of the things that I love about this is this room is the hand tool room.
- Yes, yes.
I've always intended on keeping the shop separate from the machine shop, which is in another building, and just having the hand tools in a nice quiet, you know, what I call a wood-conducive space to create.
And that way you don't have the noise of the router, you know, going on in the background and such.
- Especially with all tools, but especially with hand tools, you wanna be able to hear the sounds that they're making.
- Oh yeah.
- Because you can tell when, with a particular sound, will tell you that it's not cutting right.
- Oh yeah.
- Yeah.
- Yeah, you can hear sharp, if that makes sense.
You know, it's a wonderful sound, and it's something I can never get tired of.
And plus, the shavings coming off of those tools, very difficult to breathe those into your lungs.
You know, there's not a lot of dust.
It's shavings, and it's, you know, quiet.
And, you know, most of the cuts that we make with these hand tools are the final cuts on the chair.
So it's just a really satisfying thing to do.
- I'm sure, and I really like the fact that you teach also.
I mean, this same shop space, you'll have, what, four to six students sometimes.
- Yeah.
Yeah.
Teaching has been one of those things that's just been so rewarding.
Anytime you teach, you learn.
And if I had been making chairs by myself in a vacuum here for the last 21 years, I would've never learned what I have being able to teach.
'Cause students will make you rethink stuff that you have to explain, and then you think, "Well, I probably can come up with a better way to do that."
And so teaching has just been fantastic from that respect.
And my chairs have gotten better because of it.
And not only that, just meeting some of the most amazing people, you know, over the years has been, well, you know, really rewarding too.
- Well, you haven't always been a chairmaker.
- Right.
- How did you get started on this path?
I mean, even as a kid, was there something that you could think back that kind of started moving you on a path toward being a maker?
- Well, I've always enjoyed working with my hands, you know, from when I was a kid, you know, playing in the dirt, you know, with my dump trucks and stuff like that.
And then a lot of my early life was spent with my grandfather.
We would go to art classes and we would do oil paintings and watercolors.
And so I did a lot of, you know, artistic-type drawing with him over the years.
And when he passed away, his last car was my first car, a '68 Chevelle.
And I started just taking that apart and building that engine, and then just fell in love with the mechanics and using your hands and building engines and hearing them run.
And which led me down the path of becoming a diesel mechanic.
So for 17 years, I was an engine builder at a Volvo dealership in Nashville.
And finally, went from doing that all those years, I started going back to woodworking.
And basically, what drew me back to that was buying my first house, trying to install four pieces of crown molding that I couldn't figure out.
And then I went down that rabbit hole of buying table saws and joiners and planers and chop saws and all the typical tools you buy, you know, watching, you know, Norm Abram or somebody.
But, again, building things outta necessity.
And then one day a friend of mine asked me, he said, "Do you know what a Windsor chair is?"
And I said, "I'm not sure."
And he said he would love to have a set of Windsor chairs.
And so I started researching what was out there.
This is 2003, so not a lot on the internet, but you know, you had a few people that were teaching it.
So I went and took a class with a guy named David Wright.
He was from Berea, Kentucky, and we built a sack back chair.
And that's where my life changed, you know.
From that point forward, all I could think about was chairs.
And I remember building this first chair, which was somewhat of a disaster.
I mean, it was a crazy class, because there were way too many of us.
And I was able to get this chair built.
And I found myself sitting on the couch at night staring at this thing, like at nine o'clock at night.
Wife thought I was crazy, you know, just so enamored by this chair and this process.
And little did I know, you know, what was about to happen.
So from 2003, when I made my first chair, and you fast-forward to 2007, I had an opportunity to leave my full-time diesel mechanic job and become a full-time chairmaker.
And I had been making chairs since 2003, you know, selling them at the local craft shows and fairs and things like that.
- And these were Windsor chairs.
- Windsor chairs, right.
And also, you know, long story short, I started working with Curtis Buchanan, took a class with him, and then I started assisting him in his classes teaching; and also teaching with Peter Galbert, assisting him in his classes at Kelly Mehler's School of Woodworking.
And that was my real education in how to make chairs and how to teach chairs.
And by 2009, I built this timber-frame structure that we're sitting in here.
And after that just slowly started selling out classes and became a full-time Windsor instructor, I guess.
- Well, Greg, what makes a Windsor chair?
- Well, from what I understand, a Windsor chair basically is, think of the seat as the nucleus of everything that anchors into that seat.
So it separates the top from the bottom, the seat does.
And that's basically how you define a Windsor chair, unlike a ladder-back chair where the back leg is the back post, you know, they're connected.
So that's basically how you distinguish a Windsor chair from everything else.
- So this seat is as much of a Windsor seat as a small one or a stool, Windsor stool.
- Yeah, if you look at, you know, like, this is a sack back, a miniature sack back.
You know, the seat anchors, everything anchors into the seat and separates the top from the bottom.
And then, you know, you have different woods that you use.
And you also have different versions of the Windsor chair, which are typically named by the back of the chair or the arm or something.
- And you said this is a sack back?
- Yeah, sack back, which back in, you know, when these chairs originated from England, from what I understand, they were more garden furniture; and people would get cold, so they would drape the sack over the back of them.
And that's how it acquired the name sack back.
This is called a sack, this back bow.
So this would be the sack in this settee.
- Wow.
- This is a sac back chair blown apart to six feet wide.
- On steroids.
- It's on steroids, yeah.
- Well, in England, I remember they were painted this dark green color.
- Well, typically you would think that, because what we see now is that color, 2, 300 years later.
A lot of their colors they painted them back then were really bright and vivid because their houses were dark.
They lit with candles in the 1700s, and so their furniture was really bright so they could have color and they could see.
And then over time, the oils and the finishes and the refinishes on the chairs, they get darker.
So, you know, when we see these chairs now, we like to paint 'em representing what the antique looks like.
So we will paint 'em these dark colors, you know.
And they're basically a silhouette from across the room.
So when you look at this chair, you know, there's no one area that really represents a lot of wood grains.
So we paint 'em, because they're made from different woods.
And then you get this beautiful silhouette that just kind of goes along with a table or something that would have more natural grain and fibers in it.
- Well, this is such a small chair, but can a person sit in it, a small person, a 2-year-old?
- I'm not gonna do it, but I could stand in this chair and it would hold together.
But yeah, a 2-year-old fits perfectly in these little miniatures.
This is 50% of an actual adult-sized chair.
So it's an exact replica of what my full-sized sack back chair looks like.
- Well, wonderful.
Let's talk about some of the various woods that make up a Windsor chair.
- Okay, well, starting with the seat, which is usually a soft wood, pine, poplar, butternut, something that's easy to carve, and it's usually the driest part of the Windsor, 'cause everything else is greenwood; the turnings and all that are typically sugar maple.
You can use cherry and walnut, but sugar maple's the strongest.
And it takes really good crisp detail when you turn it.
And the hardness of these legs pierce into the soft pine, and it makes just a match made in heaven for that joint right there.
And then your upper structure, typically, is a long-grained fiber wood, like white oak or red oak, hickory, ash, something that steam-bins well, and splits and arrives and shaves with a draw knife or something, you know, that you can shape.
And so you represent the best of quality of each type of wood.
And then together, they, you know, they're just, they're perfect.
And you know, it's that.
And again, that's why we paint them so that they all kind of cohere and look good from across the room.
- Well, I can feel the tool marks, or I can feel where the tools worked.
That's something that you want to celebrate- - Oh, yeah.
- in a Windsor chair.
- Yeah, basically, the finish on these spindles, I've got some here that go in this settee.
There's 45 spindles in this settee.
But you can see the facets on here are right off of the spokeshave.
I call 'em fascinating facets, because when your hands reach and touch these things and they're just like glass, you know, they're smooth; whereas if I sanded this, it would shred the fibers, the water-based milk paint would hit that, and the whole thing would look out of focus.
So, you know, I always tell people, we sand what we don't understand.
But, you know, they'll sand the life out of something.
And it really does look out of focus.
So the spokeshave is the last tool to touch these spindles.
And it shears the fibers off.
They stay flat.
Even when the water-based milk paint hits them, they don't raise the grain.
So it's a pretty simple process.
- Well, I'm sure you make it look simple.
- Oh yeah.
It's nothing to it.
- Yeah, it takes a lot of work to make a spindle like this.
And it's made pretty much round.
- Yeah, I mean, you know, it's funny, we take round trees and we square 'em up and then we go back to round, you know.
But making something round is probably harder than it sounds.
'Cause we square these up and then we turn 'em into octagons, and every facet of an octagon, if it's the same width, then the piece will be round.
So we go from, you know, we split these out square, we shave 'em square and we shave 'em, and then we taper 'em, and then we octagon 'em, and then the last thing you do is take it round with the- - Now, this oak is something that you work green, is that correct?
- Yeah, greenwood works so much easier than kiln-dried or even dry wood.
And, you know, you can basically cut the tree down in the woods, and five days later you can have a chair.
And we split these down into small enough parts that can be dried in a kiln, a little light bulb kiln.
And we super dry 'em down to no measureable moisture content.
And when they go back into the chair, they can only, you know, increase in size.
- And the grain is very straight.
How do you get straight-grained wood?
- Well, we have to follow the grain.
That's the part of the strength of the chair.
If you think of a tree standing in the woods, it follows its own grain.
You know, it's blowing in the wind and it's, you know, straight.
So these little spindles are like individual trees.
So we've robbed those out, following that grain, which is that inherent strength- - Spreading them.
- Yes.
Yes.
- [Charles] So the grain is in control there too.
- Right, the wood wants to split down the grain.
So even if you make a spindle and it has a little bit of a curve to it, you still wanna follow that grain.
And you can manipulate 'em with heat guns and things to bend them back.
- So when you look at it, it's not completely straight, but it gives the impression of being... - Yeah, and the chair will tame 'em too, 'cause the holes you drill can redirect.
- The sack backs and the bow backs all requires some bending of wood.
- Yeah, these aren't sawn to shape.
They are straight pieces of wood that we take and we put in a steamer box, and then we bend them around the form until they dry and they stay put.
When you heat white oak, for example, it's got lignin in the wood.
And when you heat the lignin, it softens, and the wood will be pliable, like a rubber band or something.
And then when it dries, it stays put in that shape.
So steam bending is a good secret to be straight with the grain of the wood, but to make it any shape you want.
And you can bend it in both directions if you need to.
But yeah, that's a faster way.
You know, it takes like an hour to steam-bend an inch thick piece of wood.
- So you go from a steam box- - Yeah, yeah.
- to a form.
- Right.
And.
you know, you have like 45 seconds to bend it right out of the steam box.
and then you let it dry for three or four days on the form, and it's ready to go.
The heat is what actually bends the wood.
It's not the steam or the moisture; that's just simply a vehicle for the heat.
- Great, well, it also requires maybe some specialized tools that everybody doesn't know about.
- Yeah, yeah.
Hands down, my favorite tool is probably the draw knife.
It's a two-handed blade that you use to shape wood.
And they were probably in everybody's toolbox back in the '50s.
You know, I mean, it was just a common thing to have a draw knife.
And even in the 21st century, it is still the best tool to follow the grain of wood when you're shaping these little thin spindles.
The draw knife just loves to follow the grain, and so you can do quick work and shaping of wood, you know, with the draw knife.
And there's no CNC machine I know that can follow it and do it as well.
And I've got quite the collection of draw knives on my wall behind me over here.
I'm always trying to find that special geometry of a draw knife that might work a little better.
But there's a lot of different ones out there, and a lot of current makers that still make 'em, you know, still forge 'em.
- Can you show me how it works?
How a draw knife- - Yeah, absolutely.
- does this beautiful job.
- Yeah, we have to go here to the shave horse and we can do that.
- Let's go.
- Alright.
(bright folk music) (bright folk music continues) (bright folk music continues) (bright folk music continues) - In order to be able to use that draw knife, you need something to hold the stock and reference the stock while you work.
This I have something in common with: it has a dumb head.
(Greg laughs) So tell us about it.
- Well, the shave horse is what this is called.
I guess if you were in Germany it would be called a schnitzelbank.
But the shave horse is basically just a vice to hold wood and be able to move it quickly and change positions with this head; it's adjustable, and then I can work it with my foot.
And then when I let go of my foot, it falls open naturally.
So, you know, we can change positions really quickly, and then it frees up your hands.
I can hold it with my foot, and it frees up my hands to use the draw knife to shape the wood.
So quite simple.
- Sure, and you have a stick here.
- Yep, this is a piece of white oak that I have riven out with a froe, fresh out of the tree.
So this is like greenwood; you feel it's really cold and has that wet feel to it.
- Sure.
- This tree was probably standing in the woods probably a couple of months ago.
- And we interrupted its life.
- That's right.
And we're gonna give it a new life as a chair, hopefully.
So this would be spindle material.
So in use, the shave horse, you can just spin it around and shape the wood quickly.
And the draw knife is a simple tool with two handles and a blade that is fantastic at following grain.
And that's why we use a draw knife as opposed to like a hand plane or something that would ignore the fibers; the draw knife's gonna follow those fibers, whereas a hand plane would just skip over 'em and just plane through 'em.
- Oh, I can see how it's just totally valuable in turning out a spindle.
- Yes.
Yeah.
And this particular draw knife is one made by a buddy of mine down in Australia, Peter Trott.
He's actually in the States right now doing some blacksmithing courses.
But it's a fantastic tool.
You can still find these in antique stores and flea markets.
And it was probably in everybody's toolbox back in the day.
but it's an invaluable tool for chairmaking, and I couldn't do without it, you know?
- Sure, but the idea is to make it square first.
- Yes, yeah, so on a chair spindle, there are a lot of similarities between all the different chairs.
You're basically (draw knife slicing) removing the wood into a square shape.
You get it square, you're gonna taper it.
And then once you taper it, we're gonna turn it in into an octagon.
- And it's fast.
- It is.
You can lower the handles and, you know, take lots of wood off, or you can take, you know, little shavings just by raising the handles up.
So it's adjustable on the fly, and just a fantastic tool.
(draw knife slicing) - And so can you actually use that even on let's say a chair seat to make- - Absolutely, yeah.
You can use it on everything.
You can even shape your legs.
If you don't have a lathe or want to turn, you can use a draw knife to shape your legs too.
And it's fantastic at shaping the seat and the crest and your arms.
So this is like the main go-to tool for- - It's the workhorse.
- everything on the chair, basically.
So after I get done with the draw knife, we got this down into an octagon.
This is how it's gonna go into the kiln.
And I'll put it in my light bulb kiln, super dry it down to no measurable moisture content.
And then later in the week we pull it out, and I use the spokeshave to do the final.
- And then it'll be ready for the chair.
- So the draw knife, on the front edge of the seat, is where we would go to shape that.
And it's just more skewing and slicing.
(draw knife slicing) And makes quick work of shaping that.
And then you would follow that up with spokeshaves and scrapers as well.
Okay, so the travisher is the next tool after the scorp and you've done your rough excavation of the seat.
I like to go to the travisher, which is basically a scorp of the fence, a little more of a controlled cut.
And I still go cross-grain, but I push this tool instead of pull it.
(travisher slicing) And this one cuts pretty rough.
And then I can switch to this other travisher which cuts more refined, and you can hear the difference.
- [Charles] Oh yes.
- Then I can finish shaping with this scorp.
And then from there we just move to scrapers and maybe a little sandpaper if you want to.
- I enjoy the process that you've come up with.
It's traditional, but yet it has elements of new technology involved.
It's something that is ever-changing.
Makes a beautiful chair in the hands of Greg Pennington.
- Well, thank you, Charles.
Good to have you.
- I'm gonna be heading down the road to find a story of another great woodworker.
See you next time on the "Volunteer Woodworker."
(door slams) (bright folk music) (bright folk music continues) - [Announcer] "Volunteer Woodworker" is funded in part by: Since 1970, Whiteside Machine Company has been producing industrial-grade router bits in Claremont, North Carolina.
Whiteside makes carbide bits for edge forming, grooving, and CNC application: learn more at whitesiderouterbits.com; Real Milk Paint Company makes VOC-free nontoxic milk paint available in 56 colors: milk paint creates a matte wood finish that can be distressed for an antique look; Good Wood Nashville designs custom furniture and is a supplier of vintage hardwoods; Keri Price with Keller Williams Realty has been assisting Middle Tennessee home buyers and sellers since 2013; Mayfield Hardwood Lumber, supplying Appalachian hardwoods worldwide; Anna's Creative Lens, crafters of resin on wood decorative arts.
Visit CharlesBrockChairmaker.com for all you need to know about woodworking.
If you'd like to learn even more, free classes in a variety of subjects are available for streaming from CharlesBrockChairmaker.com.
(soft music) (dramatic music)
Volunteer Woodworker is presented by your local public television station.
Distributed nationally by American Public Television